📘 قراءة كتاب Guidance for Preparing Standard Operating Procedures (SOPs) E أونلاين


Page
FOREWORD ..................................................................................................................... iii
1.0 INTRODUCTION ...................................................................................................1
1.1 Overview............................................................................................................1
1.2 Purpose...............................................................................................................1
1.3 Benefits ..............................................................................................................1
1.4 Writing Styles ....................................................................................................2
2. 0 SOP PROCESS........................................................................................................3
2.1 SOP Preparation.................................................................................................3
2.2 SOP Review and Approval ................................................................................3
2.3 Frequency of Revisions and Reviews................................................................3
2.4 Checklists...........................................................................................................4
2.5 Document Control..............................................................................................4
2.6 SOP Document Tracking and Archival .............................................................4
3.0 SOP GENERAL FORMAT....................................................................................6
3.1 Title Page ...........................................................................................................6
3.2 Table of Contents...............................................................................................6
3.3 Text ....................................................................................................................6
4.0 TYPES OF SOPs .....................................................................................................8
4.1 Technical SOP Text Information Guidelines.....................................................8
4.2 Administrative SOP Text Information Guidelines ..........................................10
5.0 EXAMPLE SOPS .................................................................................................12
6.0 REFERENCES .....................................................................................................13
APPENDIX A: Preparation of Fish Tissue for Metal Analysis by ICP or Furnace AA ...14
APPENDIX B: Multiple Tube Fermentation and Most Probable Number .......................19
APPENDIX C: Waste Water Sample Collection...............................................................30
APPENDIX D: Joint Air Compliance Overview Inspection.............................................38
APPENDIX E: Preparing, Numbering, Retaining, Indexing, Revising, and Using ..........47
Standard Operating Procedures
حجم الكتاب عند التحميل : 480.9 كيلوبايت .
نوع الكتاب : pdf.
عداد القراءة:
اذا اعجبك الكتاب فضلاً اضغط على أعجبني و يمكنك تحميله من هنا:
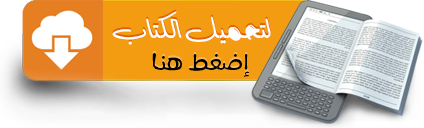
شكرًا لمساهمتكم
شكراً لمساهمتكم معنا في الإرتقاء بمستوى المكتبة ، يمكنكم االتبليغ عن اخطاء او سوء اختيار للكتب وتصنيفها ومحتواها ، أو كتاب يُمنع نشره ، او محمي بحقوق طبع ونشر ، فضلاً قم بالتبليغ عن الكتاب المُخالف:
قبل تحميل الكتاب ..
يجب ان يتوفر لديكم برنامج تشغيل وقراءة ملفات pdf
يمكن تحميلة من هنا 'http://get.adobe.com/reader/'